

The driver takes 230VAC single phase input, ie no power supply required. It has a native 160,000 count per rev encoder, 1.27Nm rated, 3.8Nm 10 sec overload at 3000rpm rated or 5000rpm max. They have very generous overload ratings, typically three to four times their rated torque.Īs an example I have a 400W B2 series Delta servo. There are some very cheap Chinese made AC servos but of questionable quality, support and documentation.ĭelta (Taiwanese manufactured in China) and DMM (Canadian manufactured in China) are two good quality brands that won't break the bank.Īny decent AC servo of sufficient power will blow ANY stepper into the weeds.
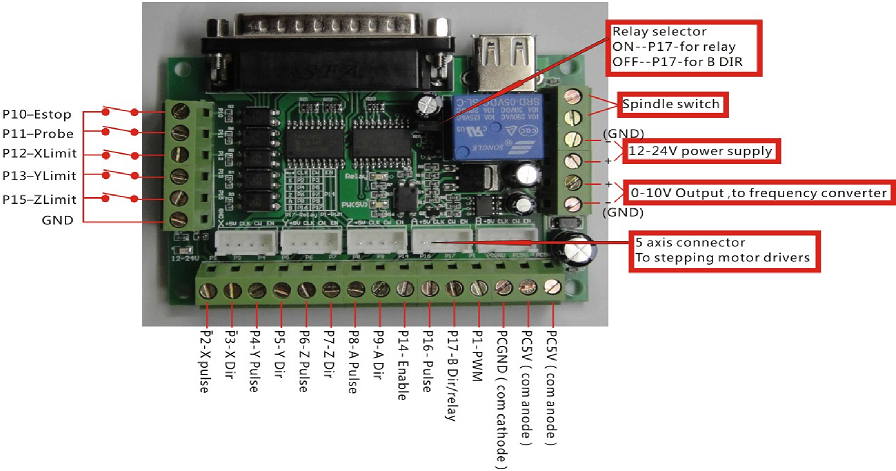
Transformer/rectifier/capacitor type power supplies are recommended over switch mode types by virtue of their superior overload capacity.ĭepending on your budget you might consider AC servos. Leadshine AM822's for example are also 80VDC capable and half the price. Gecko drivers are the gold standard for reliability but are not cheap. The effective practical maximum at this time is 80VDC. The classic means of counteracting the inductance of the windings is to use the highest possible driving voltage.

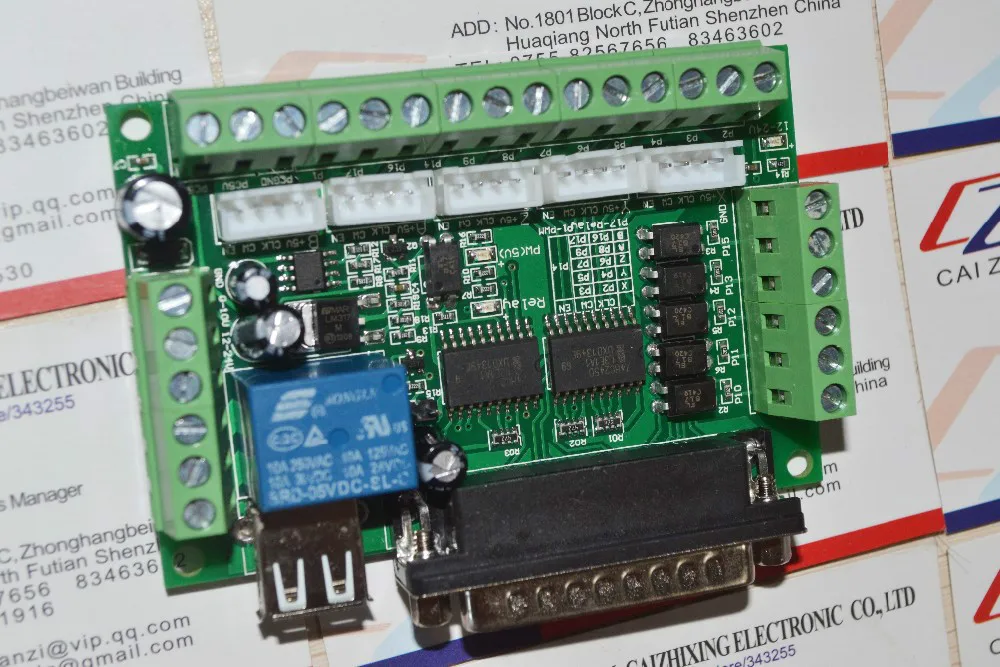
Many users have found low inductance (1-1.5mH) 23 size steppers of 350-400 oz.in outperform (overall) 34 size steppers by virtue of 34 size steppers greater inductance. With a 34 size you want 2-4mH, 2mH preferred and reject anything over 4mH. With a 23 or 24 size stepper you want 1-2mH, 1mH preferred and reject anything over 2mH. Avoid like the plague!Īll steppers lose torque the faster they go and the winding inductance determines how badly the torque will roll off with speed. These steppers have high inductance and perform Many people make the mistake of choosing 34 size steppers because of their great torque specs, say 1000 oz.in and higher. Thank you very much for your time in reading this, We understand we are complete newbies to this, so any information regarding this would be very helpful, including links to other sites or forums for help. The professor basically gave the people in the lab this task, and asked us to work from scratch, throwing us in the deep-end. finally any breakout board information is helpful as well in case the motion controller doesn't have any additional inputs for limit switches and emergency stop. Suggestions on power supplies for both motors, and motion controller would be helpful as well.Ĥ. We are currently thinking of using Nema 34 stepper motors, any suggestions in changing these motors or keeping them would be taken into consideration.ģ. If someone could suggest a good controller board for a 5 axis CNC (Mach4), that can control x y z and 2 rotary axes, along with spindle control.Ģ. I am posting a few questions, if anyone can help regarding this project, I would greatly appreciate it.ġ. Hi, I am currently a student, and am working for a university Lab that has me assisting in creating a 5 axis CNC with Mach4 software.
